Step-by-Step: How to Start Your Shipping Container Conversion Project
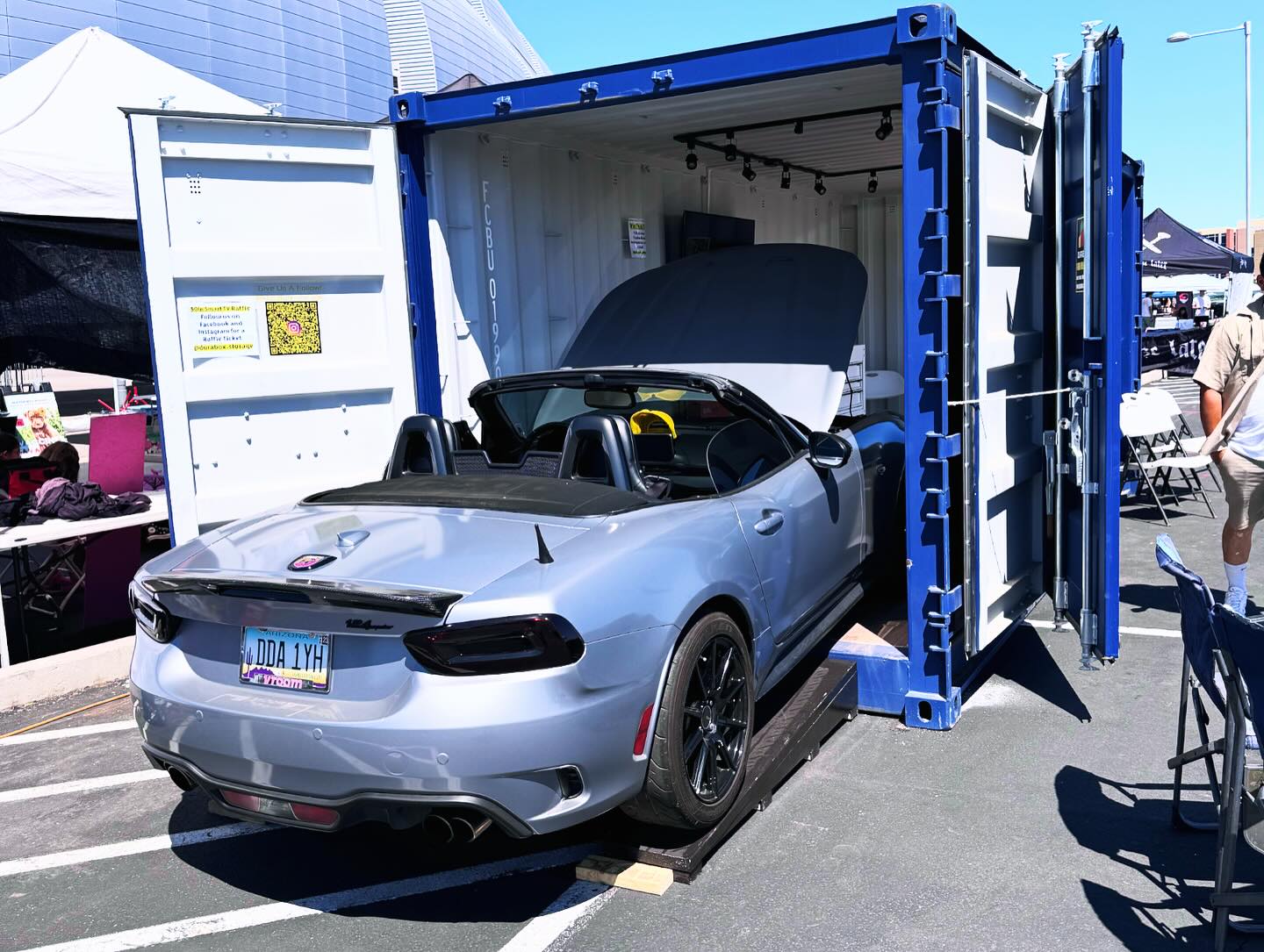
Converting a shipping container into a functional, stylish space is no longer just a trend—it’s a smart, efficient solution for those seeking durability, cost-effectiveness, and customization. Whether you’re building a mobile office, pop-up shop, personal studio, or compact home, a shipping container conversion project can deliver exceptional results with the right planning and execution.
Planning Your Shipping Container Conversion
Before the first bolt is tightened or the first panel is cut, you need a rock-solid plan. The planning stage lays the foundation for a successful and stress-free container conversion experience.
Define the Purpose
Start by defining the end goal of your shipping container conversion. Are you building a home office? A retail kiosk? A guest suite? Each use case will come with its own requirements in terms of insulation, electrical work, plumbing, and design.
Choose the Right Container Size
Shipping containers typically come in standard sizes: 20-foot and 40-foot lengths. High-cube containers (which offer extra height) are also popular for conversions that require more headroom. Make sure to select a container that suits your spatial needs and budget.
Setting a Budget for Your Conversion
Your budget will directly influence everything from design features to finishes. Consider the following line items:
- Cost of the container (new or used)
- Site preparation (grading, leveling, etc.)
- Permits and inspections
- Insulation and ventilation
- Electrical and plumbing installation
- Windows and doors
- Interior and exterior finishes
- Labor costs (if hiring contractors)
Be realistic about your budget and add a 10-15% contingency for unexpected expenses.
Sketch Your Layout
Use graph paper, software, or even a napkin sketch to envision your layout. Factor in furniture, lighting, entry points, and utility areas. A good layout helps streamline construction and reduces costly changes mid-project.
Securing Permits and Regulations
One of the most overlooked yet essential aspects of a shipping container conversion is understanding and complying with local building codes and zoning laws.
Research Local Regulations
Different jurisdictions have varying rules when it comes to alternative housing or commercial structures. Check with your local building department or zoning office to learn what permits you’ll need.
Submit Plans for Approval
Once you have a working design, you may need to submit architectural or engineering plans for approval. This process can take several weeks, so it’s best to start early.
Schedule Inspections
Inspections ensure your project meets all safety and structural requirements. Common inspections include electrical, plumbing, framing, and final walkthroughs. Keep these checkpoints in mind when scheduling your construction timeline.
Key Steps in Construction and Design
With plans and permits in hand, it’s time to begin construction. Here are the essential steps to transforming your steel box into a functional, polished space.
Preparing the Site
Before placing your container, ensure the ground is level and able to support the weight. Depending on soil conditions and intended use, you may need a concrete foundation, gravel bed, or piers.
Modifying the Container
Cutting into a shipping container requires precision and expertise. Openings for doors, windows, and HVAC units should be reinforced with steel to maintain structural integrity. Welding and grinding are common during this phase, so always prioritize safety and hire professionals if necessary.
Finding Skilled Professionals
Even if you’re taking a DIY approach, there are times when you’ll want expert help. Consider bringing in professionals for:
- Structural modifications
- Electrical and plumbing work (licensed trades required)
- HVAC installation
- Insulation and waterproofing
Collaborating with experienced tradespeople ensures your container is up to code and built to last.
Insulating the Container
Steel conducts heat and cold, making insulation vital for temperature control and energy efficiency. Options include:
- Spray foam insulation (most effective and moisture-resistant)
- Rigid foam board
- Blanket insulation (batts)
Don’t forget to insulate the ceiling and floor to prevent heat loss and moisture buildup.
Installing Doors, Windows, and Utilities
Once the container is insulated, you can install:
- Windows and skylights for natural light
- Doors (entry and interior)
- Electrical wiring, outlets, and fixtures
- Plumbing lines and fixtures (if needed)
- HVAC or mini-split systems for climate control
Be sure that all installations are sealed properly to prevent leaks and drafts.
Interior Finishing
This is where your shipping container conversion starts to feel like a real space. Common interior features include:
- Drywall or wood paneling
- Flooring (vinyl, laminate, or engineered wood)
- Cabinetry and built-ins
- Lighting and smart tech
Select durable, lightweight materials that complement the rugged container aesthetic while offering functionality.
Adding Final Touches
With the heavy lifting done, you can focus on personalizing and optimizing your space.
Exterior Treatments
Your container can be painted, wrapped, or clad in wood, metal, or composite materials for a polished exterior. Adding a canopy or awning extends your usable space and adds visual appeal.
Landscaping and Surroundings
If your container will remain stationary, consider landscaping or adding decking to create a more inviting environment. For commercial spaces, signage and outdoor lighting are key finishing touches.
Furnishing and Styling
Choose furniture that fits the compact layout. Multifunctional pieces, foldable furniture, and wall-mounted items work especially well in container spaces.
Personalize with artwork, textiles, and accessories that reflect your brand or style.
Why Choose Durabox for Your Shipping Container Conversion?
At Durabox, we specialize in high-quality storage containers and canopies designed for flexibility, performance, and longevity. Located in the heart of Maricopa County, AZ, our containers are built to thrive in the harshest conditions—making them ideal for conversion projects of all types.
Here’s why countless customers trust Durabox to kick-start their shipping container conversion projects:
- Lifetime Leak Warranty: We stand behind our products with a leak-proof guarantee.
- Local Expertise: As a local business, we understand the permitting and regulatory requirements in Maricopa County and the surrounding areas.
- Premium Containers: Our inventory includes a wide range of new and used containers in excellent condition.
- Customer Support: From planning to delivery, our team is here to answer questions and provide guidance.
So, if you’re thinking of starting your own shipping container conversion project, don’t go it alone. Let Durabox help you get started on the right foot with a dependable, durable container you can trust.
Start Your Container Conversion Journey Today
Turning a shipping container into a usable space is an exciting journey filled with creative potential. With proper planning, a bit of grit, and the right support team, you can transform a humble steel box into something extraordinary.
Ready to start your conversion project? Contact us today for a FREE quote and discover the ideal storage solution to launch your vision. Whether you’re building a workspace, boutique, studio, or something totally unique, we’re here to help every step of the way.